How does VEKA staff manage the packaging, warehousing and transportation of UPVC windows?
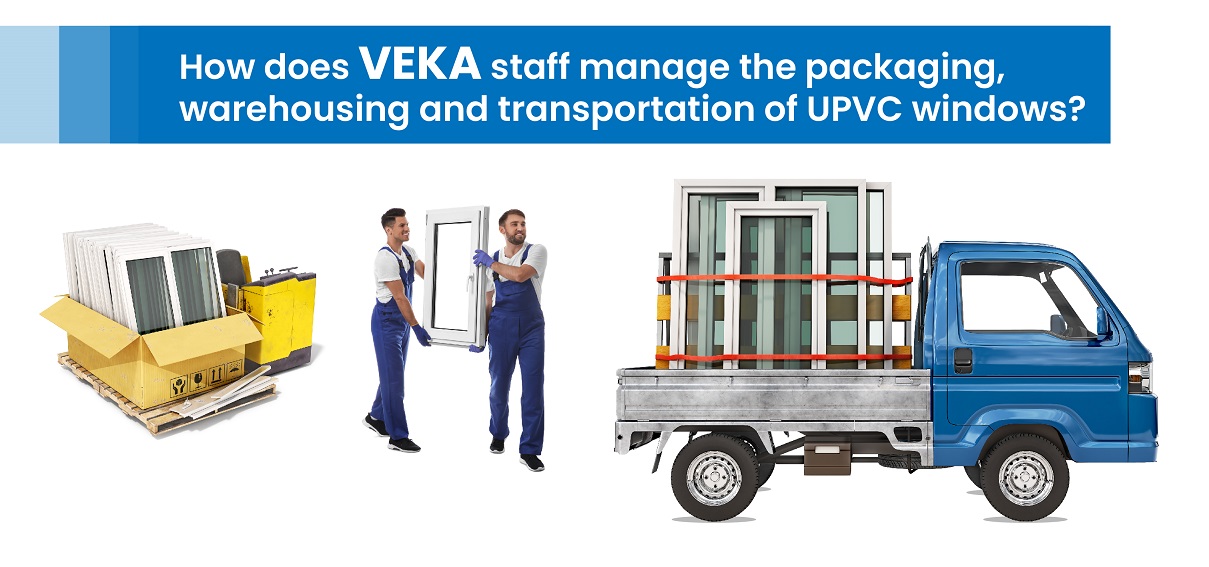
Homeowners understand the status symbol of modern uPVC windows and doors. Each piece is customised for optimal operations. At the manufacturing plant, the process begins with material selection. After uPVC windows manufacturers finish making the product, there are three advanced steps before reaching the job site for installation.
VEKA has a very sound approach to the uPVC window packaging process. It also involves warehousing and transportation. We put in effort in each step, and it is a significant part of the business to remain the market leader.
This brief manual explains the warehousing needs of finished uPVC windows. How does our team approach the packaging process? It will help the customer to learn how the quality inspection is maintained at every stage.
Overview of VEKA’s systematic approach
- How packing is done
- Warehouse storage
- Day of transportation to a job site
Packing to keep glass safe
All uPVC windows are made with tough single or double–glazed glass and then filmed with protective material. Packing assumes importance because the glass or the frames should not be scratched or stained. Often the window size is large, as in sliding or casement style. For example, French windows or large entrance doors call for the right packaging material. This ensures safety while transporting the goods to job sites very far away from the factory or warehouse. If there are more than two windows and doors to be transported, then the packaging is carefully done. The products should not be soiled or damaged in transit.
Warehousing of uPVC windows and storage
As experienced uPVC windows manufacturers, we use soft packing material to avoid the appearance of stains or spots when they are stacked together in the truck/van. All other items used are non-corrosive and will not scratch any area of the product. All the products are first sent to the warehouse if the delivery is being made to different customers. Markings are created for identification for each order. It helps the warehouse staff to avoid mistakes while loading in order of delivery.
At the warehouse:
- Storage areas are rainproof and dry. The temperature is less than 40 degrees.
- Ventilation for the products to stay in good condition.
- Our warehousing is in a pollution-free area which helps in keeping the packaging intact.
- We never store any material or frames outdoors. They are only brought out when transport is ready.
- During long storage, the windows are stacked vertically (not less than 70%) in the direction they will be installed.
- No packed product is kept on the ground level.
uPVC windows safely transport requirement
- Utmost care is required when loading and unloading. The key is to do it slowly and not throw the packed materials in the vehicle. When it is being unloaded on the job site, it is done softly.
- During transportation, the speed of the vehicle is normal. The driver has to take care of any roadblocks or emergency brakes which may shake the frames.
- No hardware touches the glass parts during vehicular movement.
- Only soft material is used to separate parts which require assembling on installation.
- Flat stacking (horizontal) is not allowed.
This quick manual will help you to understand our uPVC window packaging process, warehousing and transportation. If you wish to know about any other part of our approach to making frames or installation, do contact us.